Transfer agiler Fertigungsmethoden
Forschung trifft Praxis: Mit Transfer Zukunft gestalten
- Titel: Transfer agiler Fertigungsmethoden
- Initiator: BTU Cottbus-Senftenberg
- Laufzeit: 01/2022 – 12/2025
- Wirkungsbereich: überregional
- Förderkategorie: Wissens- und Technologietransfer
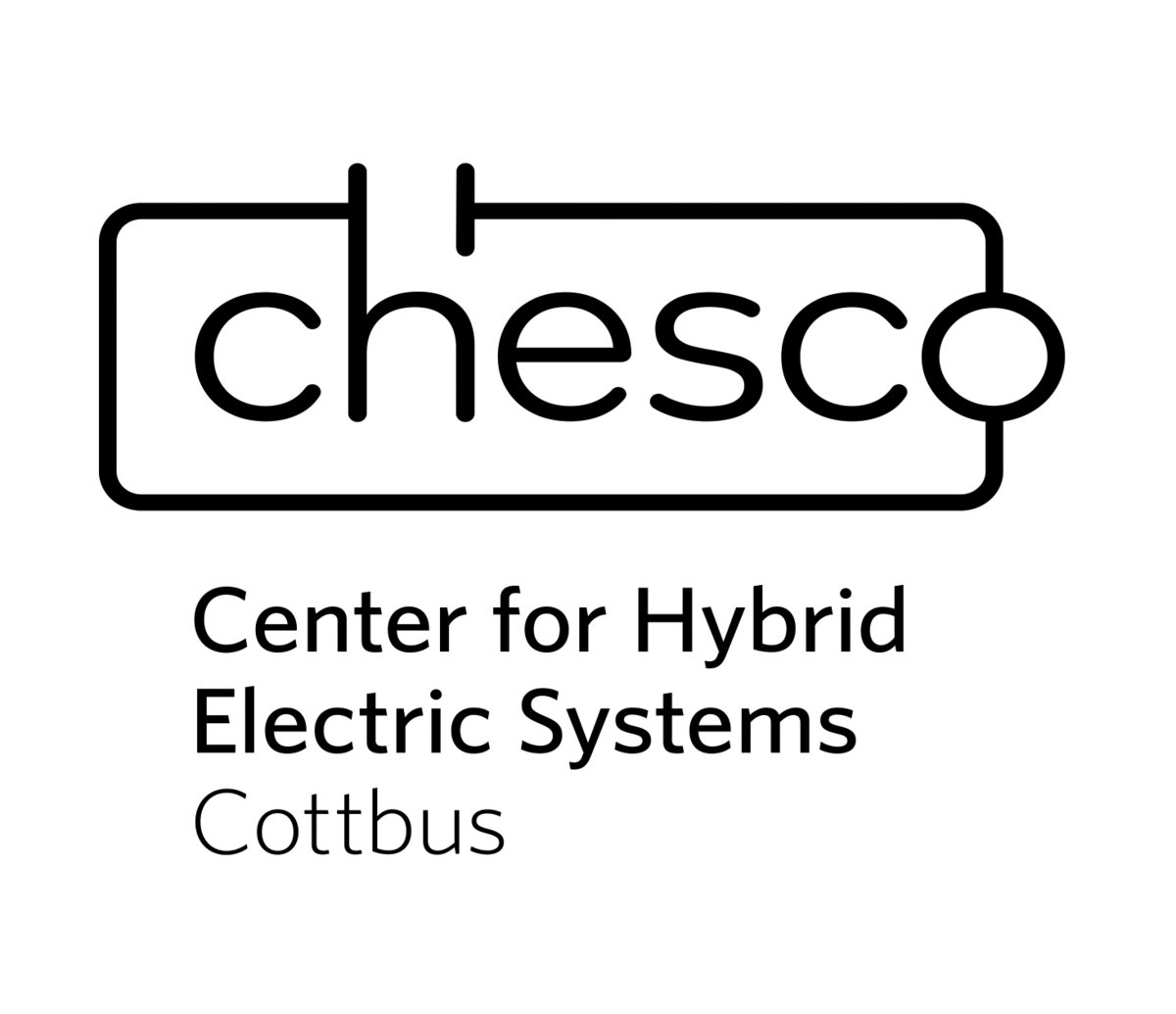
An der BTU Cottbus-Senftenberg wird seit fast 30 Jahren auf dem Gebiet der Fertigungstechnik geforscht. Damit regionale Unternehmen dieses Wissen besser nutzen können, gibt es das Projekt „taf“ (Transfer agiler Fertigungsmethoden), ein Vorhaben des Forschungszentrums chesco. Es bringt neue Fertigungsmethoden und -technologien in die Unternehmen der Region, um sie für die Anforderungen einer klimaneutralen Zukunft wettbewerbsfähig zu machen.
In diesem Projekt werden Unternehmen gezielt dabei unterstützt, verschiedene Fertigungstechnologien zu erforschen und auf modernen technischen Anlagen in der Praxis zu erproben. So können sie herausfinden, ob es eine effizientere Methode zur Herstellung ihrer Produkte gibt, ohne selbst teure Technik für den Forschungsprozess anschaffen zu müssen. Gemeinsam mit dem taf-Team haben sie nun die Möglichkeit, in einer hochmodernen Forschungsfabrik in Cottbus Prozesse unter realistischen Bedingungen zu testen und weiterzuentwickeln. Agile Fertigungsmethoden stehen dabei im Mittelpunkt: Sie zeichnen sich durch kürzere Entwicklungszyklen und den Einsatz digitaler Technologien aus und sollen die Produktion nachhaltiger gestalten. Gleichzeitig wird der Wissenstransfer durch Workshops unterstützt, in denen Unternehmen gemeinsam mit Expert*innen neue Konzepte entwickeln und anwenden.
Ein konkretes Beispiel aus dem Projekt „taf“ ist die Zusammenarbeit mit dem Lausitzer Unternehmen Orthopädie Zimmermann. In der Forschungsfabrik wurden gemeinsam alternative Herstellungsverfahren für Orthesen (medizinische Hilfsmittel) erprobt. Üblicherweise wird dazu ein Gipsabdruck des betroffenen Körperteils genommen und daraus ein Modell gefertigt – ein aufwändiges und unflexibles Verfahren. Im Entwicklungsprojekt mit dem taf-Team wurde stattdessen das betroffene Körperteil gescannt und digital bearbeitet. Anschließend wurde die Orthese im 3D-Druckverfahren hergestellt. Das spart Zeit und steigert die Qualität für die Patient*innen.
Weitere regionale Unternehmen aus verschiedenen Branchen haben sich bereits am Projekt beteiligt: vom Maschinenbau in den Bereichen Luft- und Raumfahrt und Energieerzeugung, bis hin zu Forschung und Entwicklung in der Zuliefer-, Elektronik- und Halbleiterindustrie.
Unterstützt durch ein starkes Netzwerk aus Forschungseinrichtungen und Industriepartner*innen sorgt das Projekt dafür, dass Unternehmen einen niederschwelligen Zugang zu neuen und in der Lausitz heute und zukünftig nachgefragten Geschäftsfeldern in Forschung, Entwicklung und Produktion erhalten. Gezielte Kooperationen zwischen Unternehmen und Forschungseinrichtungen führen schneller zu neuen Produkten, Dienstleistungen und Verfahren. Damit wird die Wettbewerbsfähigkeit der Lausitz gestärkt – ein wichtiger Schritt auf dem Weg zu einer nachhaltigen und resilienten Industrieregion.
Aktuelle Informationen zum Projekt finden Sie unter https://www.b-tu.de/chesco/.
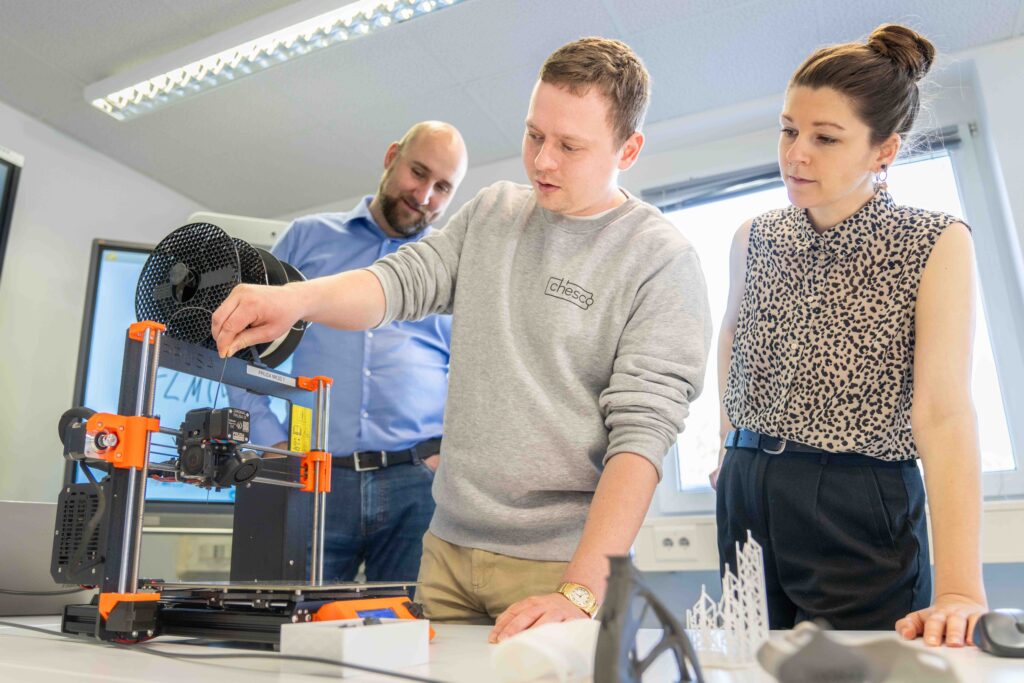
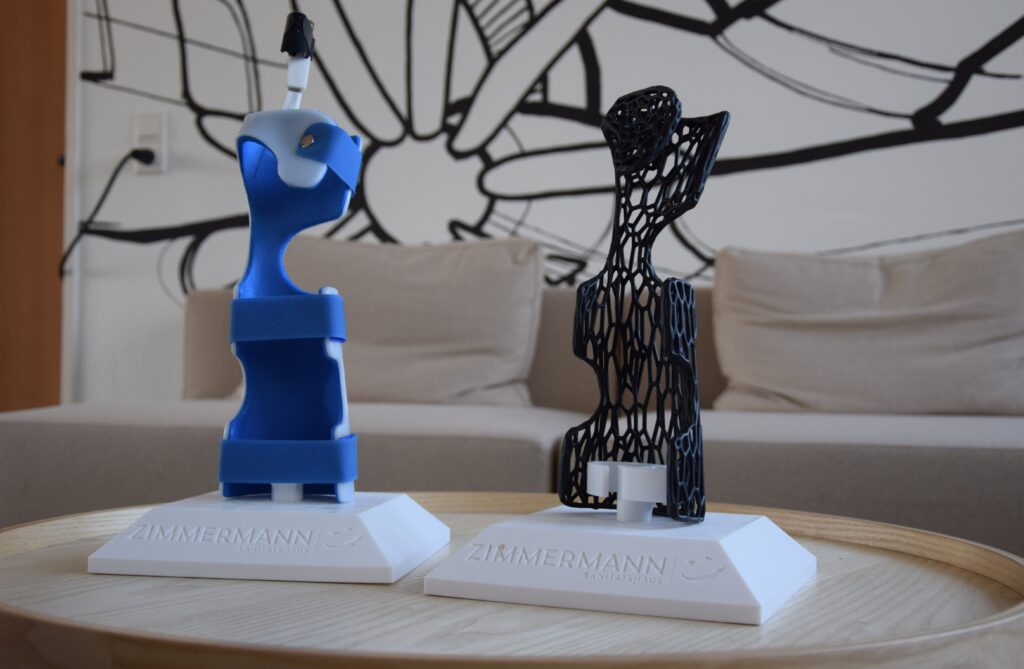
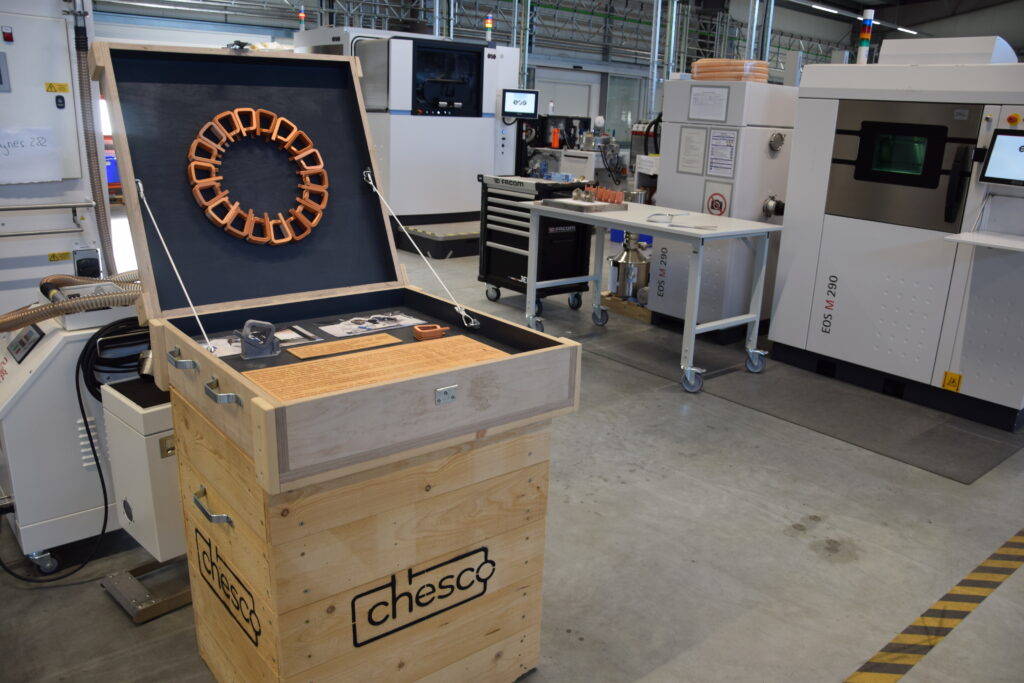